Where the Three Little Pigs Went Wrong
With forethought and planning, we can build shelters not only for safety and comfort, but also for our future and that of our environment
by Maureen Miller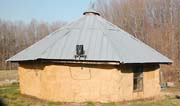
Once upon a time, our ancestors found shelter in caves. As our species ventured out, homes were cleverly formed with whatever came to hand: mud, thatch, trees, clay and even ice blocks.
Today caves are often hard to come by, and not many of us have the $277 billion William Randolph Hearst spent on his castle at San Simeon, California. Built between 1922 and 1939, it’s still regarded by Guinness as the most expensive house ever built.
The most popular material choices for home building, with some variation, remain much the same as those used by the Three Little Pigs in Joseph Jacob’s 1890 classic: straw, sticks or bricks.
The First Little Pig
The first little pig, who was more fun loving than serious, chose straw for his house. Lacking even a one-year plan, this pig wasn’t thinking long term. He was looking for a quick, easy fix, a simple shelter that would hide him from the ravages of weather and danger. The quicker he built, he theorized, the faster he could return to the real purpose of his life: playing. Spending time to look at the advantages and disadvantages of various building materials he thought a waste of time. So he chose the first commodity he came across: straw. When the danger came in the form of the wolf’s hardy breath, however, his house was easily demolished, and his fate worse.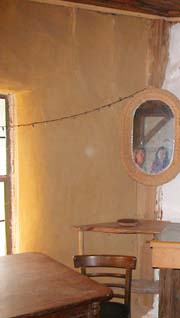
As a child, I thought this little pig was foolish, which was what Jacob wanted me to think. Why would anyone in her right mind build a house out of straw? As well as being easy to blow down, wouldn’t it also fill with mice and insects? What about heating, cooling and ventilation? Surely one couldn’t put a fireplace in a straw house. And how would you install windows?
But then I was only looking at the negatives, while others have found positives in building with straw.
Updating Straw
Straw bales were a common building material in the United States between 1895 and 1940. Interest in straw bale home construction re-emerged in the mid-1970s. Romey Pittman and Sam Droege constructed some of Anne Arundel County’s first straw bale buildings in Harwood in the late 1990s.
“It is a great building material because it’s cheap, it’s readily available, it’s environmentally sustainable, and it’s great insulation,” says Pittman.
To build with straw, you first stack the bales that will become walls, then reinforce them with rebar or bamboo stakes. There are no studs, sheathing, siding or drywall.
“This material is amenable to creating curves and shapes, which give the building so much character and depth,” says Droege.
But alone, straw bales will not stand up to the ravages of sun, rain, sleet or snow. The biggest problem that straw-bale homeowners face is keeping moisture away from the bales. Thus those who build with this material finish their structures off with plaster, mud or stucco to make them weather resistant. Droege believes that the best thing about this type of building, besides its earth-friendliness, are the mud parties.
“Mud is not caustic, like cement,” says Droege, “so everyone gets into throwing it on the walls and smearing it into the cracks.”
Mud a mixture of sand, clay and water or lime plaster is used to cover straw bale buildings inside and outside. It can be colored or painted. The result is glowing and gets more beautiful with age.
Pittman loves the earthy feel of the interior plaster as well as the beautiful colors it can take on. She cautions, however, that the plaster needs to be maintained over time and that the roof overhang must be generous enough to protect the walls.
Ease and beauty are not the only advantages to building with this material, for straw bales create their own insulating barriers. With an R rating of 40 to 50, they can provide real energy savings. Amazingly, straw bales are also fire resistant.
“It’s like trying to burn a phone book,” says Pittman. “They’re much more fire resistant than traditional stud walls, which have chimneys every 16 inches.”
Pittman theorizes that if straw bales had been the norm for homebuilding instead of wood, and someone were to go to the planning board suggesting they build a wood-framed house, the board would throw it out on the grounds of its being a fire hazard.
Today, straw-built houses are recognized within Maryland’s building codes.
One last thing about building a house with straw bales in Maryland: Not only are you saving trees, you’re also helping Maryland farmers.
“One of the most exciting things about building with straw bale today is that the straw is grown in Maryland, and purchasing it provides a market for Maryland farmers,” says Polly Bart, of Greenbuilders Inc., in Baltimore. “Greenbuilders contracts in advance with the farmer, discusses fertilizers (minimal) and pesticides (none, usually) and watches to be sure climate conditions are excellent for harvest. The resulting product is beautiful, does not harm the environment, is excellent for construction and is locally-grown. Plus, we give a permanent warranty against visits from the Big Bad Wolf.”
The Second Little Pig
The second little pig, Jacob relates, chose sticks as his basic building material. Sticks have a long history in providing human shelter. Early humans who lived near lakes or rivers often used sticks, driving them into river bottoms near the shore as support for their buildings on top.
In the 1400s, Europeans began to build half-timbered houses; when they migrated to North America, they built their shelters of logs and thatch. Following our ancestors, who settled a forested land, we build most homes from wood, at least in the Bay area.
Still, Jacob’s second little pig, who built his house of sticks, fared no better than did his brother with his house of straw.
Sticks Still a Hot Commodity
The homebuilding industry in America has had a long and profitable love affair with wood-framed houses. Quick, easy and inexpensive, this building material remains popular for the same reasons the second pig chose it.
Lately, however, we’re seeing too many similarities between the fates of our stick-built houses and the second little pig’s. Hurricanes like those that hit in Florida and New Orleans over the past several years and tornadoes like the one that struck La Plata magnify their vulnerability to Mother Nature’s huffing and puffing.
Additionally, unless sticks are treated regularly with chemicals, termites consider them their local McDonalds. Plus, let’s not forget the environment. By using wood and wasting much at job sites, we are in danger of depleting our forests. Another environmental loss: Badly insulated stick homes waste precious energy resources. Thus while the quick and easy advantages may remain, the costs of wood-framed homes are rising.
As an alternative to stick-built homes, perhaps this pig should have considered a SIP-built home. SIPs, or structural insulated panels, are basically sandwiches: foam core between two slices of oriented-strand board made of one-to-two-inch wood chips and glue. The panels can be used in building walls, ceilings, floors and roofs. The first residential development that extensively used structural insulated panels was built in 1952 in Midland, Michigan.
“The main advantages of building with insulated panels,” says Greenbuilders’ Bart, “are that less lumber is used and a high R value results, much higher than conventional framing and insulation.”
Not only do these panels have high R values, they also have high strength-to-weight ratios, making them more wind and earthquake proof than most stick built homes.
“A SIPs house or addition is quick to build, easy and inexpensive to heat and cool and quiet,” Bart says.
The Brightest Brother 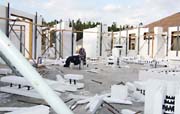
Jacob’s third little pig comes off as the smartest of the three. His brick house survives the fierce huff-and-puff test of the Big Bad Wolf. Additionally, this pig was intelligent enough to put in a fireplace, which served well in the face of danger. For when the wolf climbed down the chimney, he fell into the large pot of boiling water that the pig had hung above the fire. Voila: Wolf soup for dinner.
As strong as the little pig’s brick home with fireplace was in the face of danger, this dwelling, too, has drawbacks, for brick is not all that energy efficient, nor are fireplaces such as the pig’s.
Alternatives to brick that this little pig might consider are based on cement. Cement is an ingredient of concrete. It was used by the Greeks and Romans as a building material. But when Rome fell, so did cement. Re-discovered hundreds of years later, it became the stuff Europeans built with mainly because they didn’t have the forest resources we do in North American, but also because they learned that there is durability and strength in concrete.
Concrete is very strong and gets stronger as it ages, but, by itself, it has poor tensile strength. It doesn’t stretch or extend very well in reaction to cross-tensions. Reinforced with rebar, however, its tensile strength is increased, creating buildings that are resistant to high winds and earthquakes. Concrete alone has no insulating characteristics. But mix it with air or surround it with foam, and its insulating value increases dramatically.
Better Bricks in the Bay Area
Bay-area builders and residents are slowly discovering what Europeans have known for over 70 years. There is true value in building with insulated concrete. Plus, concrete homes have a proven track record of withstanding the ravages of hurricanes, tornadoes and fires, when all the stick-built houses around them are in ruins.
Bruce Davis Construction used Insulated Concrete Forms to build homes in the Washington Square Community of LaPlata. Davis chose this material for three reasons: increased insulating value, decreased sound transmission and increased fire safety.
Insulated concrete forms are typically made from rigid foam plastic insulation, the stuff of coffee cups and meat trays. They are designed to hold concrete in place during the initial pour and remain in place to provide thermal insulation. The forms are stacked, much like Legos, the concrete is poured between the foam panels and rebar is added to give the walls strength.
In September 2002, The U.S. Department of Housing and Urban Development evaluated the construction at Washington Square and found that overall residents had a favorable opinion. Residents cited several attributes: increased energy/monetary savings, overall durability, increased acoustical value and enhanced visual appeal. Residents liked the deep-set windows walls are 12 inches thick and felt safer inside their ICF home during hurricanes and tornadoes. Energy bills were half the cost residents paid in conventional buildings.
John Spears, an architect and president of the Sustainable Design Group in Gaithersburg, built his passive solar home out of Autoclaved Aerated Concrete block three years ago. He’s found only positives in building with this material.
“It’s not only fire-, wind- and rot-proof,” Spears says. “But also bugs don’t eat it, it’s nonpolluting and it breathes.”
He says the lightweight blocks are easy to work with and can be stacked free-form to create interesting curves. What’s more, the resulting 12-inch thick walls provide handy window seats.
Autoclaved aerated concrete has been commonly used in European construction since the late 1940s. As air makes up 80 percent by volume of the material, it has 10 times the insulating value of commercial concrete. The blocks have a flat surface that looks like hard, fine sponge. Like a sponge, they absorb water easily and thus must be protected from moisture: usually with stucco on the outside and plaster on the inside.
Energy Efficient: Building for the 21st Century
I doubt that the term energy efficient existed in the days of the little pigs. Had it, Jacob may have described specific aspects of the pigs’ houses, like windows, hot water heaters, heating and cooling systems, lighting and appliances.
If the third pig, with energy efficiency in mind, were to make modifications to his home today, what might he consider? Here are some possibilities.
Tankless water heaters provide hot water on-demand, eliminating that big storage tank and its associated standby losses. Tankless heaters have either an electric or gas heating mechanism activated by turning on the hot water faucet. Once activated, the heater provides a continuous supply of hot water, which stops as soon as you turn off the faucet. Folks from England, as well as their neighbors on the Continent have been using tankless water heaters for years. Since water heaters are recognized as the second leading energy user in the home, I’ll bet that the third pig would have investigated this potential savings in his home upgrades.
Solar sky tubes, or tubular skylights, admit sunlight for illuminating interiors without the drawbacks of conventional skylights, such as leaking, unevenly distributed light and carpets faded by UV exposure. Sky tubes are generally easier to install and do not require construction of an insulated, finished well, as do conventional skylights. With electric lighting the third largest consumer of energy in buildings, it’s a safe bet that the third pig would have looked into sky tubes.
Or for a few more dollars, he could opt for radiant floor heat. Radiant floor heat is created by laying pipes under the flooring; 120-degree water circulates through the pipes. Those who have gone to the additional trouble and cost of heating their homes or individual rooms this way report the savings to be considerable and the comfort to be unbelievable.
The Moral to the Story
As the third pig had just set out to make his fortune, he might have had insufficient cash to make these modifications. But, surely as smart as he was, he would have looked for ways to cut his energy usage and corresponding bills. To this end, he would have used some tried-and-true strategies: good insulation, high-quality windows, weather proofing, eliminating leaks from ductwork, using programmable thermostats and looking for the Energy Star rating when purchasing new appliances.
The moral to this story? With a little forethought and planning, we can build and maintain our shelters not only for safety and comfort, but also for our future and that of our environment.
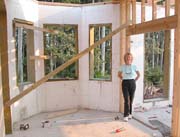 |
About the Author
Maureen Miller and her husband Craig are building their new home in Georgia with Insulated Concrete Forms for several reasons. First, the destruction they witnessed due to high winds from hurricanes and tornadoes made them realize they wanted a house that wouldn’t blow down. Second, they wanted a more bug-proof home. Third, they wanted to use materials that would do a better job of heat transference, keeping the house cooler in the summer and warmer in the winter.
|